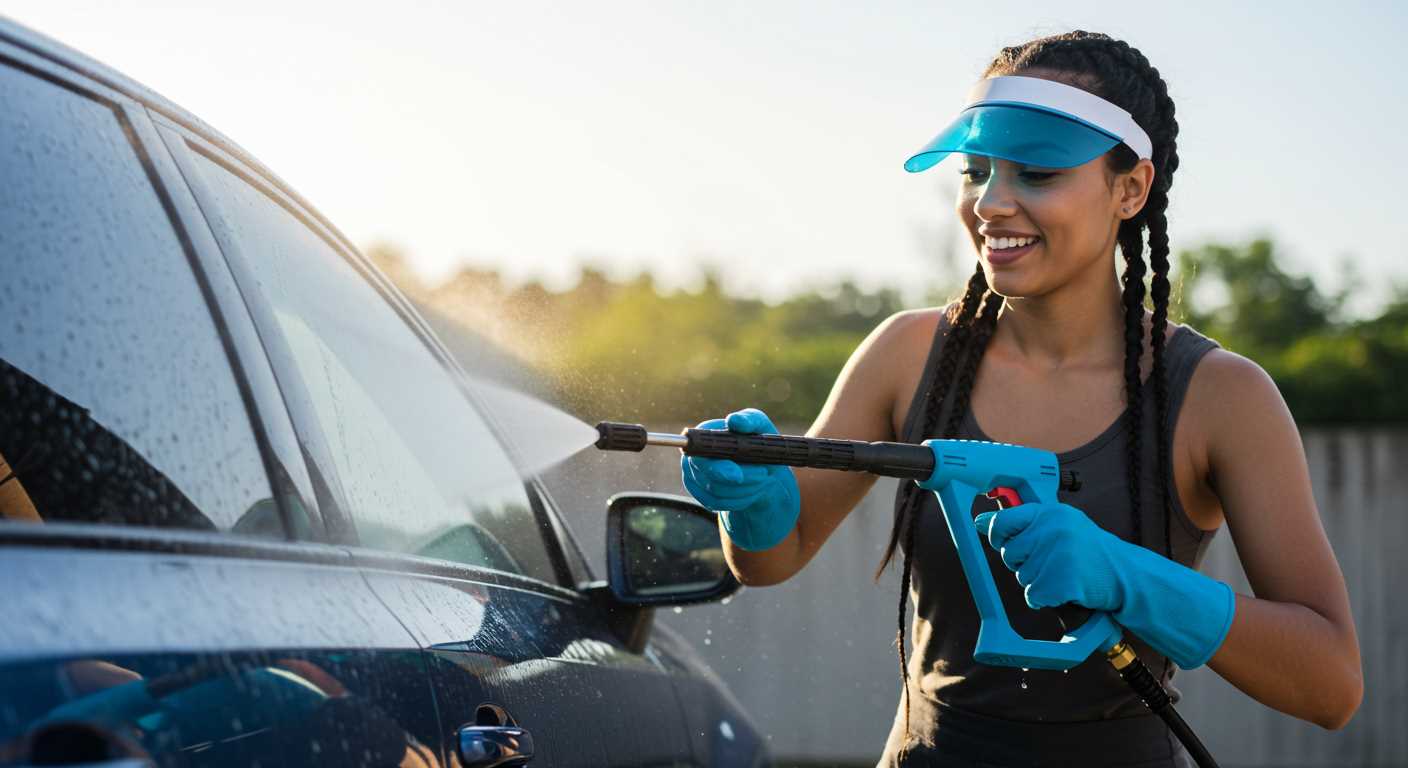




To stand out in the high-pressure cleaning industry, acquiring recognised qualifications is key. I recall the moment I decided to elevate my skills beyond mere operation. It was a rainy afternoon, and I noticed how much more efficient my methods became after attending a specialised workshop. The knowledge gained from that experience was invaluable.
First, seek out accredited training programmes that focus on high-pressure equipment operation and safety procedures. I remember attending a local training session where hands-on experience with various models taught me nuances that manuals often overlook. Engaging with seasoned instructors allows for real-time insights and tips that you won’t find in textbooks.
Next, invest in practical experience. Volunteer for community projects or offer your services at discounted rates to gain exposure. I spent weekends helping local businesses clean their facades. The feedback and referrals I received not only honed my skills but also built my reputation within the community.
Finally, stay updated with industry standards and innovations. Subscribe to relevant publications and join forums where professionals share their experiences. I’ve often found that the most valuable lessons come from discussions with peers who have faced similar challenges. This continuous learning approach has kept my techniques sharp and relevant.
Understanding the Role and Responsibilities of a Pressure Cleaner
Every operator must grasp the significance of safety measures. Always wear protective gear, including goggles and gloves, to shield yourself from flying debris and chemical splashes. My first day on the job, I neglected this and ended up with a nasty scratch from a loose stone. Lesson learned.
- Equipment Knowledge: Familiarity with various models is vital. Each type, from electric to gas-powered, has distinct features and operational methods. I recall struggling with a particularly stubborn unit until I took the time to read the manual thoroughly.
- Surface Assessment: Identifying the correct settings for different surfaces is crucial. For instance, using a high-pressure setting on wood can cause damage. I once ruined a deck by not adjusting the pressure, which was a costly mistake.
- Chemical Usage: Understanding cleaning agents is key. Not all surfaces react well to the same chemicals. During a job, I chose an inappropriate chemical that caused discolouration on a client’s patio. Always test a small area first.
- Customer Interaction: Communication is paramount. Clients appreciate clear explanations of the work being done and potential outcomes. I make it a point to discuss what they can expect, which builds trust and satisfaction.
Efficient water usage is another responsibility. Waste not only affects the environment but can also inflate costs for clients. On one occasion, I developed a technique to optimise water flow, which impressed the customer and saved them money.
Finally, keep records of your projects. Documenting the equipment used, techniques applied, and customer feedback is invaluable for future jobs. I still refer back to my notes from previous jobs for troubleshooting and improving my methods.
Researching Certification Requirements in Your Region
Start by visiting your local government or regulatory authority’s website. Often, they provide detailed guidelines on training programs and necessary qualifications for operators in this field. I recall navigating through my state’s department of labour resources, where I found invaluable information regarding the prerequisites for licencing. Each region has its own criteria, so ensure you gather specifics that apply to your area.
Exploring Training Options
Look into accredited training centres that offer courses tailored to your needs. I took a course that combined both theoretical knowledge and practical hands-on experience. This not only boosted my confidence but also ensured I understood safety protocols and equipment operation. Additionally, some organisations offer online modules, which can be convenient if you have a busy schedule.
Networking with Industry Professionals
Connecting with experienced individuals in the cleaning sector can provide insights into the certification process. Join local workshops or forums where you can ask questions and learn from their experiences. I remember meeting a seasoned cleaner at a trade show who shared tips on the best deck cleaner to use with pressure washer equipment. Such interactions can be both informative and motivating.
Finally, keep track of any changes in regulations. Subscribing to industry newsletters or joining associations can be beneficial. This will ensure you stay updated on any new requirements or training opportunities that arise.
Selecting the Right Training Program for Certification
When seeking a training programme for certification, prioritise those that offer hands-on experience. In my early days, I attended a course where the emphasis was solely on theory. While I learned the basics, it wasn’t until I got my hands dirty with actual equipment that everything clicked. Look for courses that integrate practical sessions with knowledgeable instructors.
Investigate the credentials of trainers. A course led by someone with extensive industry experience, like I had, can significantly enhance your learning. Instructors who have worked in the field can provide insights that textbooks simply cannot. Ask about their background; a trainer who has used various models and techniques will give you a broader perspective.
Check the course curriculum. Ensure it covers the latest techniques and safety protocols. I once attended a session that included outdated methods, which could lead to potential hazards. A good programme should also focus on environmental considerations and the proper use of cleaning agents. Look for content that includes both mechanical understanding and eco-friendly practices.
Consider the flexibility of the training schedule. Many people juggling work or other commitments need options that fit around their lives. Online courses can be beneficial, but ensure they still provide opportunities for live interaction and feedback. Personal engagement can be invaluable.
Read reviews and testimonials from past participants. I often rely on feedback to gauge the effectiveness of a course. Engaging with former students can give you a sense of what to expect and whether the programme aligns with your goals. Don’t hesitate to reach out and ask about their experiences.
Lastly, evaluate the overall cost versus the value you will gain. While some programmes may be more expensive, they often provide superior resources and networking opportunities. In my career, the connections I’ve made through training have been as valuable as the knowledge itself. Make your decision based on long-term benefits rather than just upfront costs.
Gaining Hands-On Experience with Pressure Washing Equipment
To truly master the art of high-pressure cleaning, hands-on experience is non-negotiable. I vividly recall my first encounter with these machines; it was exhilarating yet daunting. The sheer power they wield can be intimidating for newcomers. My advice? Start small and gradually work your way up to more complex tasks. Seek opportunities to volunteer or work with established companies that offer cleaning services. This exposure will provide invaluable insights into equipment handling and maintenance.
Understanding Different Equipment Types
Familiarity with various models and their specific functions is vital. Spend time experimenting with electric and gas-powered devices, as each has its own advantages and limitations. I remember working with a commercial-grade unit that boasted adjustable pressure settings, which allowed me to tackle everything from delicate surfaces to stubborn grime. Document your experiences with each type; note what works best for different applications. This knowledge will serve you well in the field.
Maintenance and Safety Practices
Proper maintenance is key to maximising equipment lifespan and efficiency. Regularly check for leaks, clean filters, and ensure the nozzles are clear. I once neglected a simple nozzle cleaning and ended up with uneven spraying, which cost me a job. Safety protocols should also be at the forefront of your mind. Always wear protective gear, including goggles and gloves, and be aware of your surroundings. I’ve had moments where a simple lapse in attention led to minor injuries; these incidents are easily avoidable with diligence.
Task | Frequency | Notes |
---|---|---|
Check oil levels | Before every use | Essential for gas models |
Clean filters | Weekly | Prevents clogging |
Inspect hoses and connections | Before each job | Look for wear and tear |
Test pressure settings | Before each use | Adjust based on surface type |
Engaging with experienced technicians will also accelerate your learning. Don’t hesitate to ask questions; most are happy to share tips and tricks from their experiences. Building a network in this field can lead to mentorship opportunities and further hands-on training.
Learning About Different Types of Pressure Washers
Choosing the right cleaning unit is crucial for any aspiring technician. I remember my early days when I faced the daunting task of selecting equipment. Each type of machine serves a unique purpose, and knowing their differences can save time and enhance results.
Electric vs. Gas Models
Electric machines are perfect for light-duty tasks around homes, like washing vehicles or cleaning patios. They are quieter, lighter, and easier to handle. I often used these for residential jobs where noise levels mattered. However, the power is limited, so they won’t tackle heavy-duty grime.
Gas-powered units, on the other hand, are your go-to for tougher jobs. These machines deliver higher pressure and flow rates, making them suitable for commercial applications. I once cleaned a large warehouse with a gas unit, and the difference in efficiency was remarkable. The downside? They require more maintenance and can be cumbersome to transport.
Hot Water vs. Cold Water Units
Understanding the water temperature is another key factor. Cold water units suffice for most standard tasks, like removing dirt and mildew. During my time, I often relied on these for general cleaning. However, hot water machines excel in eliminating oil-based stains and grease. I recall a particularly challenging job at a restaurant where the hot water unit made quick work of baked-on grease. The right temperature can significantly impact your cleaning success.
In summary, familiarising yourself with these variations not only optimises your performance but also enhances customer satisfaction. Choose wisely based on the demands of each task, and you’ll find your work becomes more efficient and rewarding.
Familiarising Yourself with Safety Protocols and Best Practices
Before you handle any high-pressure equipment, understanding safety protocols is non-negotiable. I’ve seen too many individuals overlook this aspect, leading to accidents that could have been easily prevented. Always start with personal protective equipment (PPE). Invest in high-quality goggles, gloves, and non-slip footwear. These basics can protect you from flying debris and chemical splashes.
Key Safety Measures
- Always inspect your equipment before use. Check for wear and tear on hoses and connections. A faulty hose can burst under pressure, causing injury.
- Maintain a safe distance from surfaces. Each type of surface requires a different distance to prevent damage. For example, concrete can withstand high pressure, while wood can splinter.
- Never point the nozzle at yourself or anyone else. This may seem obvious, but accidents happen in the heat of the moment.
- Be aware of your surroundings. Look out for children, pets, or fragile items nearby. Set up barriers if necessary.
Best Practices for Operation
When operating any washing unit, adopt a systematic approach. Start from the top and work your way down. This ensures that dirt and grime flow downwards, making your job easier. Also, keep the nozzle moving to avoid damage from concentrated pressure on a single spot.
Another aspect I’ve learned over the years is the importance of using the right cleaning solutions. Not all surfaces respond well to the same cleaning agents. For instance, using bleach on painted surfaces can lead to peeling. Always read labels and follow manufacturer recommendations.
- Keep a first aid kit handy. Accidents can still happen, so be prepared to address minor injuries.
- Stay hydrated. Operating at high pressure can be exhausting, especially in warmer weather.
- Maintain a clean work area. Clutter can lead to slips and falls, so keep your space tidy while you work.
Throughout my career, I’ve often been reminded that safety doesn’t take a back seat in this field. By prioritising these protocols and practices, you not only protect yourself but also contribute to a safer working environment for everyone involved.
Preparing for the Certification Exam: Study Tips and Resources
Focus on the exam syllabus. I spent hours going through the outline provided by the certifying body; it helped me understand what to expect and where to concentrate my efforts. Each section highlighted key topics that I needed to master, from equipment functionality to cleaning techniques.
Utilise practice exams. These were invaluable during my preparation. They familiarised me with the format and types of questions I would encounter. I recommend setting aside time each week to take a practice test under exam conditions. This not only builds confidence but also identifies areas needing improvement.
Join study groups or forums. Sharing insights with peers can clarify complex topics and offer different perspectives. I found local study groups where we exchanged tips and resources, which made the process less daunting and more engaging. Online forums are also great for connecting with others in the field.
Leverage online resources. Numerous websites and platforms offer tutorials, videos, and articles dedicated to the specifics of the cleaning industry. I particularly enjoyed watching demonstrations of equipment in action, as it reinforced theoretical knowledge with practical applications.
Focus on safety protocols. Understanding safety measures is crucial. I made a checklist of the most common safety practices and reviewed it frequently. This not only helped me during the exam but also ingrained these practices into my routine when working with high-pressure systems.
Lastly, don’t forget to take breaks. Overloading your brain can lead to burnout. I scheduled regular intervals during my study sessions to rest and recharge. This approach kept my mind sharp and ready to absorb new information.
For a quick mental break, I often turned to cooking. If you’re looking for something simple, check out this guide on how long to put potatoes in pressure cooker.
Obtaining Liability Insurance for Your Pressure Washing Business
Securing liability insurance is a crucial step for anyone launching a cleaning service. From my experience, it’s not just about compliance; it’s about protecting yourself and your investment. I remember my first project; I was so focused on the work that I overlooked the potential risks. A small mishap led to a damaged property, and I quickly realised how important insurance was. Without it, I would have faced hefty costs.
When looking for coverage, start by assessing the specific risks associated with your service. Consider factors such as the type of surfaces you’ll clean, the equipment you use, and the environments you operate in. For instance, if you handle delicate materials or work around high-end properties, your insurance needs may differ from those who mainly service commercial spaces.
Contact multiple insurers to compare policies and quotes. I found that some companies specialise in coverage for cleaning businesses, which can offer tailored solutions. Pay attention to the fine print; ensure the policy covers bodily injury, property damage, and legal fees. I once missed a key exclusion in a policy, which led to unexpected costs down the line.
Don’t hesitate to ask questions. Insurers can provide insights into what typical policies cover and help you understand any gaps. Additionally, engaging with fellow entrepreneurs in the cleaning industry can yield valuable recommendations for reputable insurance providers. Networking can save you time and money.
If you plan to hire employees, ensure your policy includes worker’s compensation. This protects both you and your staff in case of accidents. I learned this the hard way after a colleague slipped while washing a slippery surface. The insurance saved us from a lot of trouble.
Lastly, review your policy annually. As your business grows or changes, your coverage should adapt accordingly. I found that adjusting my insurance as I expanded my services not only provided peace of mind but also safeguarded my business from unforeseen events.
Building a Portfolio and Marketing Your Services Post-Certification
Start by compiling a portfolio showcasing your work. Document before-and-after images of your projects. This visual evidence speaks volumes. Include a variety of jobs, from residential to commercial, to demonstrate versatility. I remember one project where I transformed a grimy driveway into a pristine surface; the client was thrilled, and that job became a highlight in my portfolio.
Next, create an online presence. A simple website will suffice–include your portfolio, services offered, and contact information. Use social media platforms to share progress shots and engage with potential clients. When I began promoting my services, I found that Instagram attracted a lot of attention. High-quality visuals of my work reached more people than I anticipated.
Leverage local community forums and groups. Join platforms like Facebook or Nextdoor, where your neighbourhood might seek recommendations for cleaning services. I often posted in local groups, offering tips on maintaining surfaces, which helped establish my reputation before securing jobs.
Networking is invaluable. Attend local business events or trade shows related to home improvement or landscaping. I met several contractors who began referring clients to me, simply because I took the time to build relationships. Collaborating with other service providers can also open doors to new projects.
Offer promotions or discounts for your first few clients. This not only helps build your client base but also generates word-of-mouth referrals. I still remember the first discount I offered; it resulted in a cascade of new clients who were eager to share their experiences.
Lastly, ask for reviews. After completing a job, don’t hesitate to request feedback. Positive testimonials can be powerful tools for attracting new customers. I would follow up with clients via email, thanking them for their business and kindly asking if they could leave a review on my website or social media pages. It made a difference in my early marketing efforts.
FAQ:
What qualifications do I need to become a certified pressure washer?
To become a certified pressure washer, you typically need to complete a training program that covers various aspects of pressure washing, including safety procedures, equipment operation, and cleaning techniques. Many certification programs also require you to have a high school diploma or equivalent. Some employers may prefer or require additional certifications in areas such as environmental safety or specific equipment handling.
How long does it take to get certified as a pressure washer?
The duration of certification programs for pressure washers can vary widely. Some courses can be completed in just a few days, while others may take several weeks, especially if they include hands-on training and assessments. It’s important to choose a program that fits your schedule and offers the depth of training you need to feel confident in your skills.
Are there any specific tools or equipment I need before starting a pressure washing certification course?
Before starting a certification course in pressure washing, it is advisable to have basic personal protective equipment (PPE) such as gloves, safety goggles, and sturdy footwear. Some training programs may provide equipment for you to use during the course, but having your own pressure washer and accessories can be beneficial for practical training and self-study.
What topics are typically covered in pressure washer certification training?
Certification training for pressure washers usually includes a variety of topics. Key areas often covered include the types of pressure washing equipment and their functions, safety protocols, chemical handling and application, surface cleaning techniques, and customer service skills. Some courses may also touch on environmental regulations related to water usage and chemical discharge.
How can I find a reputable certification program for pressure washing?
To find a reputable pressure washing certification program, you can start by researching local trade schools or vocational training centres that offer courses in this field. Online reviews and testimonials from former students can provide insights into the quality of the program. Additionally, checking if the program is recognised by industry associations can be a good indicator of its credibility.