

Pressure washer troubleshooting and repair doesn’t have to be difficult and you can solve many common problems on your own. My guide will show you how.
Most max psi washer contraptions, especially the ones that I recommend on this site, are very well built, durable, reliable, and are constructed of high quality parts. However, despite your best efforts, you may run into some problems with your power washer from time to time. Most of these problems can be solved very easily on your own, however in some cases you may need to take your unit in to have it serviced. The following are some common problems that may crop up and what you can do to solve them.
Petrol Pressure Washer Repair. Troubleshooting Your Gas Powered Machine.
Petrol power clean-up devices require a bit more maintenance than electric washers because of their engines. Also petrol machines are able to produce much more pressure than electric models, which is good, but with additional pressure and power comes the potential for more issues. The good thing though is that you can take care of most of these yourself.
Problem | Cause | Solution |
---|---|---|
1. Pump won’t produce pressure or the pressure is erratic and pulsing, or the water volume is low. | 1. Faulty pump | 1. Take your washer in to get it serviced or check out the video below on how to repair it yourself. |
2. Blocked nozzle | 2. Clean the nozzle by first disconnecting the gun and the spray wand. Then use a small piece of rigid wire, like a straightened paper clip to clean out any debris from the nozzle. Then flush some water backwards through the wand to make sure it’s clear. | |
3. Leaky spray gun | 3. This can’t be repaired; you’ll have to replace it. | |
4. High pressure hose leaks or is blocked. | 4. Clear the blocks or replace the hose. | |
5. Water supply is too hot (over 100 degrees F). | 5. Use colder water. | |
6. Inlet hose screen may be clogged. | 6. Check the inlet hose screen and clean it out if needed. | |
7. Leaking, kinked or blocked inlet garden hose. | 7. Unkink or unblock the hose, patch it, or get a new one. | |
8. Insufficient water supply. | 8. Increase the water flow. | |
9. You have a low pressure nozzle attached. | 9. Replace the nozzle with a high pressure one. | |
2. When you add load to the engine it slows and gets bogged down. | The engine may simply be set at a slow speed. | Move the throttle up to a faster position. If the engine still runs slow then you’ll need to take it to a service center. |
3. Engine won’t start, starts and won’t run smooth, or cuts off while it’s running. | 1. It could just be out of gas or low on gas. | 1. Fill ‘er up. |
2. The oil is low. | 2. Fill up the crankcase with oil to the right level. | |
3. Air filter is dirty. | 3. Clean or replace the air filter. | |
4. Fuel may be stale. | 4. If you didn’t properly winterize your washer then this is likely. You’ll need to drain the fuel tank and fill it with fresh fuel. | |
5. Spark plug is not properly connecting to the spark plug wire. | 5. Connect the wire to the spark plug. | |
6. Water in the fuel. | 6. Drain the fuel tank and fill it with fresh fuel. | |
7. Burnt out spark plug. | 7. Replace the spark plug with a new one. | |
8. Fuel mixture may be too rich. | 8. You’ll have to take the washer in for service if this is the case. | |
4. No power from the engine. | Air filter is blocked or dirty. | Clean or replace the air filter. |
5. The cleaning solution won’t mix with the water spray. (This only applies to you if your pressure washer siphons cleaning solution from a bucket outside the unit.) | 1. The high pressure nozzle is installed. | 1. You need to switch to a low pressure, high spread nozzle tip, or if your nozzle is adjustable, turn it to a low pressure setting. |
2. The siphoning tube for the detergent is not submerged. | 2. Stick the tube down into the detergent. | |
3. The siphoning tube is cracked or clogged up. | 3. Unclog it, clean, or replace it. | |
4. The cleaner siphoning check ball is stuck. | 4. Unstick or free the check ball. |
Below is a fantastic 2 part video series that diagnoses the cause of a common power scrubber tool problem, low pressure, and tells you how to fix it. I knew nothing about the inner workings of a gas power cleaner pump before watching this and now I think I could actually take one apart and repair it myself.
Electric Pressure Washer Repair. Troubleshooting Your Electric Powered Cleaner.
Electric washers are pretty easy to operate and maintain and you’ll find that you won’t have a lot of problems with most of them. However there are some problems that may crop up from time to time. Here are some common ones, with their causes and solutions. Your Owner’s Manual should have more detailed information about your particular model.
Problem | Cause | Solution |
---|---|---|
1. Motor will not start. | 1. Problems with the plug. | 1. Switch to another plug or press the reset button on the GFCI plug. |
2. Power switch not turned on. | 2. Just flip the switch on. | |
3. Not enough power coming from the electrical outlet. | 3. Switch to a different outlet. | |
4. Tripped circuit breaker. | 4. Turn your washer off. Let the machine cool off and then attempt to restart again. | |
5. Extension cord not supplying enough power. | 5. Upgrade your extension cord to one that matches the power needs of your washer. | |
2. Water pressure is variable, coming out hard then slow. | 1. Water inlet supply is insufficient. | 1. Turn the water on to full power and check your garden hose for leaks, blockage, or any kinks. |
2. Water inlet filter is blocked. | 2. Remove the filter and clean it using warm water. | |
3. Pump is sucking air. | 3. Make sure all of the fittings and hoses are secure and air tight. Cut your washer off and purge the air out of the pump by pulling the nozzle gun until the water flows steadily out of the tip. | |
4. The spray gun or hose may be calcified. | 4. Use the cleaner suction tube to run distilled vinegar through the washer. | |
5. Nozzle is blocked. | 5. Remove debris or buildup with a fine needle. | |
3. Strong pressure is not reached. | 1. Spray wand is set to the low pressure setting. | 1. Simply switch the wand to a higher setting, or change the tip to a higher pressure one. |
2. Blocked water inlet filter. | 2. Take out the filter and rinse it off under warm water. | |
3. Not enough water coming in. | 3. Turn the water up to the maximum. | |
4. Water supply is limited. | 4. Check your garden hose for blockage, leaks, or kinks. | |
5. Garden hose diameter is too thin. | 5. Replace the hose with a larger one. | |
6. Garden hose is too long. | 6. Replace with a shorter garden hose or remove the extension hose if you’ve added one. | |
4. The cleaning solution is not coming out. (The causes here apply to machines that have built-in detergent containers.) | 1. The discharge nozzle is clogged or blocked. | 1. Remove the debris using a fine needle. |
2. Wand it set to high pressure or you have a high pressure tip in place. | 2. Change the tip or adjust the spray wand to a low pressure with a wide spray angle. | |
3. The cleaning solution suction tube is blocked or damaged. | 3. Clean out the suction tube and remove any debris, or replace it with a new one. | |
4. The filter on the detergent suction tube is clogged up. | 4. Remove and clean the filter with warm water to remove any debris. | |
5. Detergent or cleaning solution is too thick. | 5. Mix the detergent with water to dilute it. | |
6. Cleaning solution suction tube is not properly connected to the washer. | 6. Check the connection. | |
5. Spray wand leaks. | 1. The wand is not correctly attached to the washer. | 1. Make sure the wand is inserted and turned correctly to ensure a tight connection. |
2. Broken or damaged o-ring. | 2. Replace o-ring or call the manufacturer’s customer support. | |
6. Garden hose connection leaks | 1. Not screwed on tightly enough. | 1. Screw the hose on tighter |
2. Rubber washer is missing or worn out. | 2. Replace with a new washer. | |
7. Noisy pump. | Pump is sucking air. | Check and make sure all of the hoses are screwed on tight. Turn the washer off and squeeze the trigger gun until a steady stream of water comes out so that all of the air is out of the pump. |
8. Oil is dripping. | Oil seals are worn down or damaged. | Call the manufacturer’s customer support. |
9. Pump is leaking water (less than 10 drops per minute is OK). | 1. Fittings or hose connections are loose. | 1. Tighten everything up. |
2. Water seals are worn or damaged. | 2. Replace the seals or call customer service for more information. |
Some Usage Tips to Help Prevent Potential Damage
I have another article on this site about How To Use A High-Intensity Scrubbing Engine Safely and Effectively. By following the advice found there you can prevent a lot of potential problems that may crop up. Here are a couple more suggestions on keeping your pressure washer in tip top shape.
As you can see from the troubleshooting lists of this article, a common problem with high intensity cleaner mechanisms is a lack of water pressure. If you’ve tried some of the solutions listed and still don’t have any luck, then the problem may lie in your water source.
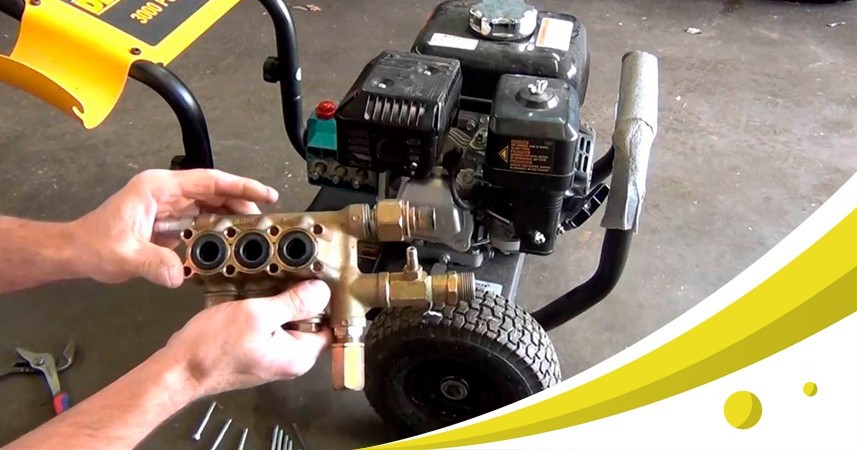